New to farm safety and not sure where to start? We've got a guide made just for you.
Get to know the difference between a SWMS and a SWP, and more!
Talk to a safety person about documents and it’s a fair bet they will drop an acronym or two in the conversation, expecting everybody to understand what they mean. Knowing what they all mean, the difference between them and when to use which one is pretty easy once it’s been explained, so let’s do that.
The first thing to point out is that sometimes the same type of document can have a few different names, none of which are right or wrong. In your operation, use whatever works for you.
Some of the common terms you may hear are:
Policy – a document that outlines the business’ objectives and view for WHS. It is generally a higher-level document approved by the CEO or most senior person and may set some high-level objectives.
Procedure – procedures provide the specific methods for the day-to-day operations of the organisation.
SOP – Standard Operating Procedure – this is a step-by-step document for performing a task or using machinery and equipment.
SWP – Safe Work Procedure – this is a ‘how to use’ document and focusses very much on safety when performing a task or using machinery and equipment.
SWI – Safe Work Instruction – same as above for SWP.
JSA / JSEA – Job Safety (Environmental) Analysis – similar to a SWP, this document looks at the hazards of a task or using a piece of machinery or equipment
SWMS – Safe Work Method Statement – these are specific to the construction industry, in particular high-risk construction. A SWMS is a document that breaks a job down into steps, and risk assesses each step of the process.
What do I use and when?
All businesses should have an active, current WHS Policy outlining the expectations around WHS in the operations. There could be a range of other policies as well, such as Fit for Work which could include statements for alcohol and other drugs, fatigue management, mental health etc. Policies around incident reporting, bullying & harassment, grievances, wearing PPE and a range of other things are advisable also.
Set up procedures as to how you want things done day-to-day. It may be as simple as a checklist, or a more detailed document outlining processes and contingencies.
In agriculture, we use a lot of machinery and equipment, which makes our lives much easier than having to do everything manually. With this comes risk, so before using or letting others use equipment, make sure you’ve done everything reasonably practicable to reduce that risk. Creating documents is a lower level control in managing risk, but still an important one.
We often get asked about the difference between a Safe Work Method Statement (SWMS) and other kinds of documents (SOP, SWP, SWI, JSA etc.). Quite simply, a SWMS only needs to be used in high risk construction. A helpful factsheet is available from Safework Australia to explain when a SWMS is needed, and when it’s not. There are some minor differences between Australian states on things like the risk of falling from a height – for example some states have 2m and others use 3m as the height which creates High Risk Construction Work. Make sure you check your local regulations.
You will probably have construction work on your property from time to time, for example building a new shed, putting up new silos etc. Chances are the construction will be carried out in an area where ‘there is movement of powered mobile plant’ – this means you have high risk construction work so you must ensure a SWMS is developed. If you’re getting someone in to do the construction, the contractor you use must complete the SWMS in consultation with you and anyone else involved in the project. If you’re doing the work in-house, you need to ensure someone completes the SWMS.
Unless you are doing high risk construction work*, I suggest don’t bother with creating a SWMS as this is a more detailed process and document. They are great documents and not really that difficult to do but for most of what you do on-farm, SWMS are a bit over the top and not necessary.
Putting SWPs in place for your machinery and equipment is the smart option if used in conjunction with other controls to manage risk. Examples of other controls include regular maintenance, ensuring guarding over moving parts is in place, and people using the equipment are trained and competent. Check out the 4 Steps to Risk Management to know what you need to be doing.
When you need to create a SWP, SOP, SWMS or whichever document you need, there are plenty of templates available. You can create your own from scratch, or Safe Ag Systems has a suite of SWP templates for most of machinery and equipment you would use. With over 200 agriculture specific templates available, we’ve got you covered for most things.
* This information is taken from Safework SA website and provides a good overview. Check your local regulator’s website for state-specific information.
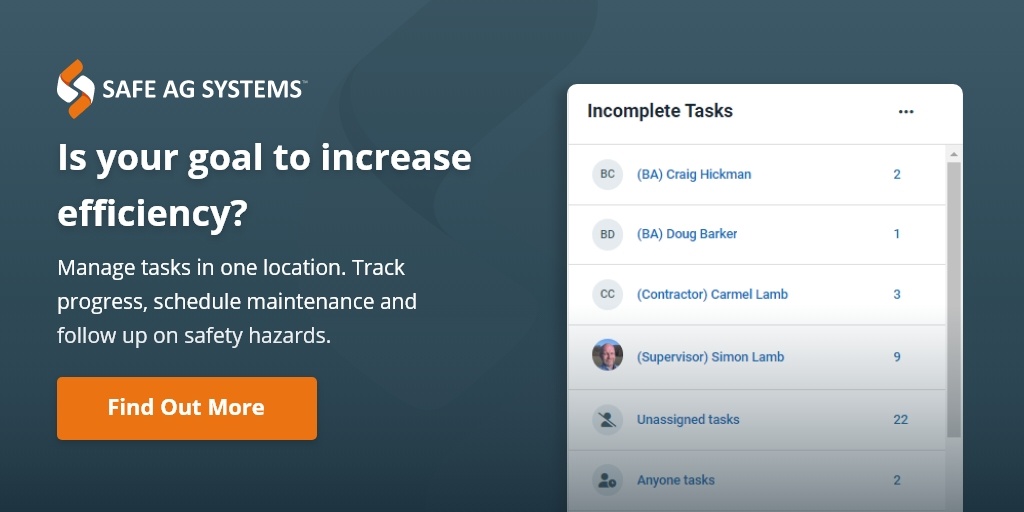
Disclaimer: Content on this website may be of relevance to users outside of Australia, but content links and examples are specific to Australia. Please check with your local authority for your country and industry requirements.